Before
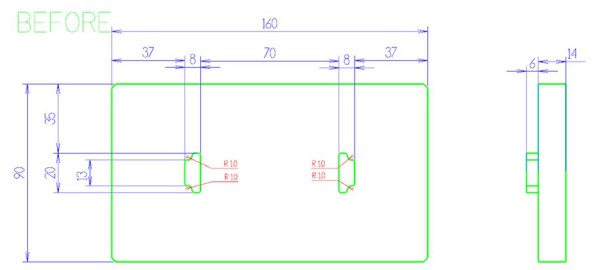
今回お伝えするマシニング・フライス加工品のVE設計提案事例は、突起部(島残し部)についてです。まずはBefore図や下記の3DCADをご覧ください。このプレートには2つの突起部が設計されていますが、それぞれ高さ6.0mm、内R部が1.0mmとされています。
こうした突起部(島残し部)についてフライス加工の観点から申しますと、この設計は切削コストがどうしても高くなってしまいます。というのも、外Rを切削する場合にはエンドミルなどの刃物の径は問題になりませんが、内Rの場合はそのRに合わせた刃物を選定することが必要になります。今回のケースで言うとφ2のエンドミルを選定する必要があります。
小さな刃物を選定すればいいだけではないか?とお考えになるかも知れませんが、実はそうではありません。問題は高さ(深さ)です。φ2のエンドミルではおおよそ2d(=4mm)までが限界であり、高さ6.0mmの突起部を削り出すとなると、時間をかけて少しずつ削らなければならず非効率になります。さらに、刃物の折損リスクも高まります。
コストダウン事例
After
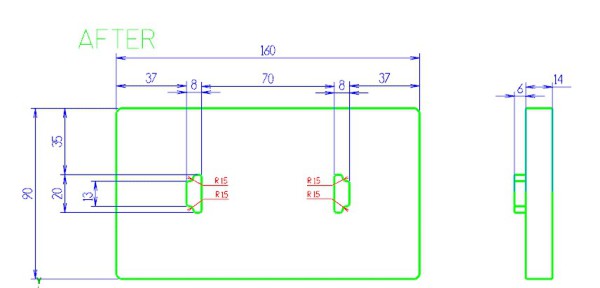
こうした突起部(島残し部)の設計にあたっては、できれば高さ(深さ)を考慮して内Rの大きさを決定します。例えばR1.0をR1.5という具合に設計変更を行うことができれば、使用するエンドミルはφ2ではなくφ3が使用できます。φ3のエンドミルであれば、高さ6.0mmは難なく加工ができるので、先述の切削加工時間や折損リスクの問題が解消でき、結果としてコストダウンに繋がります。
今回の突起部(島残し部)の内Rについては、設計段階においてここまで配慮することはなかなか難しい部分がありますが、機械加工+溶接.comを運営する三栄製作所にお声掛け頂ければ、様々な角度からのVE提案をさせて頂くことができますので、お問合せください。
ちなみに今回のケース(内R1.0→R1.5)が仮にステンレスだった場合は、加工時間としては下記となります。
全部R1.0 粗取り5分+仕上げ10分 → 15分
全部R1.5 一発加工で5分、刃物折損リスク、精度も向上
なお、内Rが小さい場合は特に配慮する必要があります。エンドミルφ2の場合は、2dつまり4mmが限度と申し上げましたが、φ10のエンドミルであれば3d・4dでも加工することが可能です。
ちなみに今回のケース(内R1.0→R1.5)が仮にステンレスだった場合は、加工時間としては下記となります。
全部R1.0 粗取り5分+仕上げ10分 → 15分
全部R1.5 一発加工で5分、刃物折損リスク、精度も向上
なお、内Rが小さい場合は特に配慮する必要があります。エンドミルφ2の場合は、2dつまり4mmが限度と申し上げましたが、φ10のエンドミルであれば3d・4dでも加工することが可能です。